A CIMON Xpanel HMI lets users manage on-site pumps and tanks. Different screens allow engineers to view status and alarms, as well as diagnose and test pumps during maintenance. A CIMON PLC takes in data from sensors and outputs electrical signals to the pumps.
Water Plant Case Study
Case Study from | CIMON
WBUD Water Project (Case Study)
With funding from the Tennessee Valley Authority, Watts Bar Utility District (WBUD) needed to streamline the automation of its 32 tank and pump stations. System integrator Quality Controls LLC decided to use PLC, HMI, and SCADA products from CIMON to automate these facilities.
.
At each location, a CIMON Xpanel HMI lets users manage on-site pumps and tanks. Different screens allow engineers to view status and alarms, as well as diagnose and test pumps during maintenance. A CIMON PLC takes in data from sensors and outputs electrical signals to the pumps.
A program automatically switches between different modes of operation, allowing for schedule-based or level-based control. The PLC also acts as a bridge between devices by storing, receiving, and sending data. When a malfunction occurs, the PLC sends a warning signal to both the SCADA program and the local HMI.
Radio transmitters were integrated into the network to overcome the immense cost and communication difficulties of laying wire through mountainous terrain. Data values are sent to a central location, then processed by the UltimateAccess SCADA application. User requests are then sent back over the radio to the corresponding PLC, which performs the desired action. The combined usage of PLC, HMI, and SCADA technologies from CIMON allows WBUD to more effectively manage its pump and tank stations.
The content & opinions in this article are the author’s and do not necessarily represent the views of ManufacturingTomorrow
Comments (0)
This post does not have any comments. Be the first to leave a comment below.
Featured Product
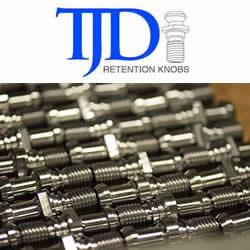